News Story
AHX-PI Lab Develops Novel Polymer Composite Heat Exchanger
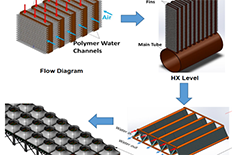
Under the direction of Minta Martin Professor Michael Ohadi and Research Associate Farah Singer, the Advanced Heat Exchangers and Process Intensification (AHX-PI) Laboratory at the University of Maryland, College Park has successfully developed a novel Polymer Composite Heat Exchanger (CHX). This heat exchanger is enabled by a Novel Additive Manufacturing technique to yield superior thermal performance at reduced pressure drops and with substantial weight reduction when compared to state of the art corresponding heat exchangers. The effective thermal conductivity of this polymer heat exchanger is ~115 W/(m-K), which is record high.
The current design, generation III (Gen III) printer has a speed well over 200 times faster than its first generation (Gen I). Future designs call for additional boost in the production speed. This Advanced Research Projects Agency-Energy (ARPA-E)-supported heat exchanger technology has diverse thermal management applications and a demonstrated potential to introduce transformative changes to the way heat exchangers are designed and fabricated.
AHX-PI’s CHX consists of polymer channels through which the water passes, and metallic wires, which pass through the hot and cold flow to act as the heat transfer medium. The main advantages of the CHX compared to conventional technology such as fin-and-tube heat exchangers are (1) its low weight and low cost, as the channels are made of polymer; (2) the excellent corrosion resistance of the polymer that encapsulates the metallic wire; (3) its high performance, as the heat is transferred from hot flow to cold flow through the metallic wires directly connecting the two mediums; (4) enhanced heat transfer, as the wire behaves like pin fins, which generally yield higher heat transfer coefficients than conventional louver fins; and (5) fabrication as a single component using Additive Manufacturing, which eliminates the need for welding/brazing and additional tooling.
The CHX was fabricated using a first of its kind additive manufacturing method developed and patented by the AHX-PI team. Starting from an off-the-shelf Fused Deposition Melting (FDM) additive manufacturing machine, the team created and added a new printing head capable of laying down the metallic fibers of the CHX. The fabrication method of the CHX is automated, performed by an additive manufacturing machine composed of two heads, one printing the polymer channels and the other laying down the metallic fibers.
AHX-PI developed three generations of this machine, where Gen I and Gen II are composed of one polymer head and one metallic head, each. With these machines, various CHXs up to 1Kw were fabricated and experimentally tested to successfully validate the performance predictions. AHX-PI, then developed the Gen III which is a multi-head machine capable of printing 10 polymer channels at once and laying one full layer of 45 metallic fiber at once. Gen III is almost 200 times faster than Gen I and capable of printing a 20kW CHX in about 6 hours.
At the U.S. Department of Energy ARPA-E summit, AHX-PI was invited to present the composite polymer heat exchanger in a showcase to all summit attendees. For more information, visit http://www.arpae-summit.com/Agenda/Summit-Agenda.
To hear more about the project, listen to the team's interview with Voice of America: https://www.voanews.com/a/three-d-printing-heat-exchangers/4308249.html.
Published August 24, 2018